Physical ore beneficiation technologies
REE ores are rocks or unconsolidated sediments made up of a number of minerals, including REE minerals such as monazite, bastnäsite, xenotime, eudialyte and steenstrupine, and gangue minerals such as quartz, feldspar or calcite. Depending on the form and location of the orebody, REE ores may be mined by either open pit (surface) or underground methods.
Beneficiation is the term used for the processing of the raw ore to remove gangue minerals, producing an REE concentrate that can then be shipped for further processing. The EURARE project aimed to optimise beneficiation for European REE ores and to minimise the environmental impacts. Beneficiation methods vary from deposit to deposit, and are dependent on the grain size, mineralogy and texture of the ore. These characteristics are different for every REE deposit, and therefore the ore has to be carefully studied before testing.
Where the ore is coarse in grain size, it can be crushed coarsely and it may be possible to concentrate the minerals using physical methods such as gravity or magnetic separation. Finer grained rare earth minerals need to be separated using methods such as froth flotation, which absorb a specific collector on the surface of the rare earth minerals to allow a physical separation. Complex ores may not be suitable for beneficiation and require direct, whole of ore leaching in order to recover the rare earth elements.
Beneficiation testwork in EURARE
The first step for the EURARE project was to carry out bench-scale testwork to develop beneficiation methods for several European REE ores. By September 2014, beneficiation methods had been developed for ores from Kvanefjeld, Kringlerne and Norra Kärr, with promising results from the Olserum and Fen deposits. Following this, the EURARE project carried out pilot-scale testing of these methods, at a beneficiation plant at GTK in Finland. The first ore for testing, from Kvanefjeld, was delivered to GTK in August 2014. A pilot plant run using the Kvanefjeld ore was successfully carried out in April 2015, producing REE concentrates with 15% REO. Mixed REE carbonates were then produced from these REE concentrates at Outotec, Finland, and delivered to the EURARE partners for REE extraction in October 2015. Beneficiation pilot plant runs were also successfully performed on ore from Norra Kärr and Kringlerne during 2015.
Beneficiation of ore also produces a waste product, known as tailings. As part of the EURARE project, the tailings produced by the beneficiation testwork will be characterised and closely monitored to investigate any potential environmental impacts. In general, the REE tailings do not contain sulphide minerals and therefore do not generate acid mine drainage. Levels of radioactivity are low, but in some cases may be above background.
A summary of all the beneficiation testwork carried out in the EURARE project can be found here
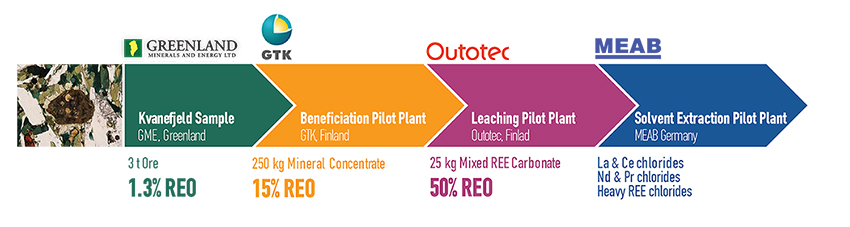